経済的発注量分析
材料を購入してから消費するまでに発生する在庫関連費用は、発注費と保管費からなります。
発注費は、材料の発生から入庫までに必要となる原価で、発注のための通信費、文房具、送料、倉庫への搬入費用などがあります。
保管費は、材料の在庫を維持するために発生する金利、保険料、倉敷料、陳腐化の費用などがあります。
材料が必要になった時に発注すれば、保管費は安く済みます。しかし、材料が必要になった都度発注すると、発注回数が増えて発注費が多くかかります。
一方、1回当たりの発注量を増やせば発注回数が減るので、発注費を安くできます。しかし、1回当たりの発注量が増えることで、材料の在庫量も増え保管費が多くかかります。
つまり、発注費と保管費の間には、発注費を安くすると保管費が高くなり、保管費を安くすると発注費が高くなるという関係があります。
そこで、発注費と保管費を合計した在庫関連費用が最も少なくなる1回当たり発注量を分析することが、在庫管理には重要となります。この在庫関連費用が最も少なくなるように1回当たり発注量を分析することを経済的発注量(EOQ)分析といいます。
経済的発注量の計算
発注費と保管費の関係をグラフに表すと以下のようになります。
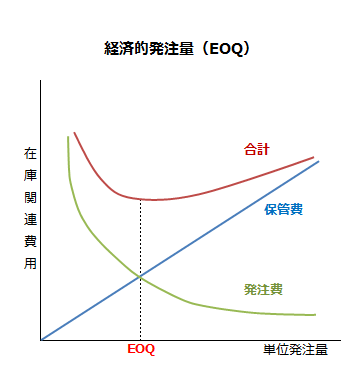
発注費の総額は、材料の総需要量を発注回数で除し、その値に1回当たり発注費を乗じた価額となります。
- 発注費総額=総需要量/発注量×1回当たり発注費
一方の保管費の総額は、平均在庫量に単位当たり保管費を乗じた価額となります。ここで平均在庫量は、発注量に2分の1を乗じて計算します。
- 保管費総額=発注量/2×単位当たり保管費
したがって、在庫関連費用は以下のように計算できます。
- 在庫関連費用=発注費総額+保管費総額
在庫関連費用を少なくするためには、発注費総額と保管費総額の合計が最も少なくなるように1回当たり発注量、すなわち経済的発注量(EOQ)を決定しなければなりません。
経済的発注量は、以下の式で計算できます。

例えば、在庫関連の資料が以下のように与えられていたとします。
- 1回当たり発注費=10,000円
- 年間1個当たり保管費=300円
- 年間総需要量15,000個
上記計算式に当てはめて、経済的発注量を計算すると1,000個となります。
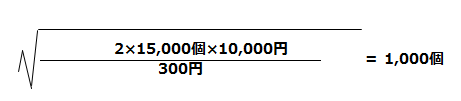
経済的発注点分析
材料を消費していくと、やがて在庫切れを起こします。在庫切れを起こすと生産が止まってしまうので、在庫切れを起こす前に材料を発注しなければなりません。
発注してすぐに材料が到着することは滅多にありません。到着には、1日、3日、1週間、1ヶ月など、一定期間を要するのが通常です。そのため、発注から到着までにかかる期間を事前に見積る必要があります。
材料の発注点は、補充期間における材料の見積消費量まで材料が減少した時点となります。例えば、補充期間が3日で、その間の材料消費量が150個であれば、保管している材料が150個まで減った時点で発注をかければ、生産が止まることはありません。
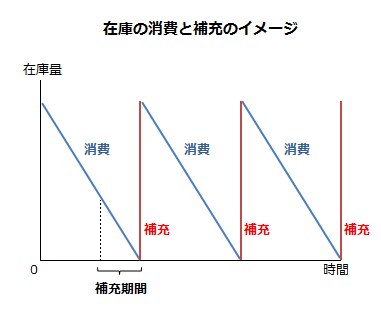
しかし、現実の経営において、需要量を正確に算定することは容易ではありません。ある時、いつもより多くの受注があった場合、材料の消費量をギリギリに見積もっていたのでは、対応できないことがあります。
そこで、需要見込みが間違っていた場合でも大きな損失が発生しないように安全在庫を保持しておくことが大切です。
そうすると、最適な発注点は、補充期間の見積消費量に安全在庫量を加えた数量となり、このような発注点を経済的発注点(EOP)といいます。
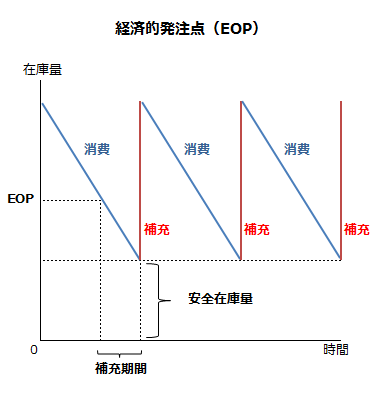
ここで、材料をどれだけ補充するかが問題となりますが、これは、経済的発注量分析で計算した数量となります。
また、安全在庫を保持することは、余分に保管費がかかってしまいますが、それは一種の保険料としての性格を有していると言えます。
安全在庫をどの程度保持するかは、その保管費と品切れ損失とを比較して決めることになります。品切れのために失った利益(機会損失)、追加注文に関わる費用、顧客の不満のコストが品切れ損失と考えられますが、その見積りは主観的になりやすい点に注意しなければなりません。